Pourquoi les industries doivent-elles optimiser leur consommation énergétique ?
Dans un contexte marqué par la hausse continue des coûts de l’énergie et l’urgence climatique, optimiser sa consommation énergétique n’est plus une option mais une nécessité stratégique pour toute entreprise industrielle. Les procédés thermiques, qu’il s’agisse de chauffe, de refroidissement, de séchage ou de traitement de fluides, représentent une part significative des dépenses d’exploitation. Pourtant, dans de nombreux sites de production, une quantité importante de chaleur fatale est encore rejetée sans être valorisée, alourdissant inutilement la facture énergétique globale. Parallèlement, les réglementations environnementales imposent aux industriels des objectifs de réduction des émissions de CO₂, les incitant à investir dans des solutions plus sobres et plus durables. C’est dans cette logique que s’inscrit l’optimisation thermique, avec des leviers techniques concrets comme la récupération de chaleur, la production en ligne plutôt qu’en batch, l’isolation thermique des réseaux, la réorganisation des réseaux thermiques. Dans chacun de ces objectifs, le bon dimensionnement d’un échangeur thermique peut être critique. Mieux gérer les flux d’énergie dans un process industriel, c’est non seulement réduire les coûts, mais aussi améliorer la compétitivité, renforcer la résilience face aux fluctuations du marché de l’énergie, et répondre aux exigences RSE de plus en plus pressantes.
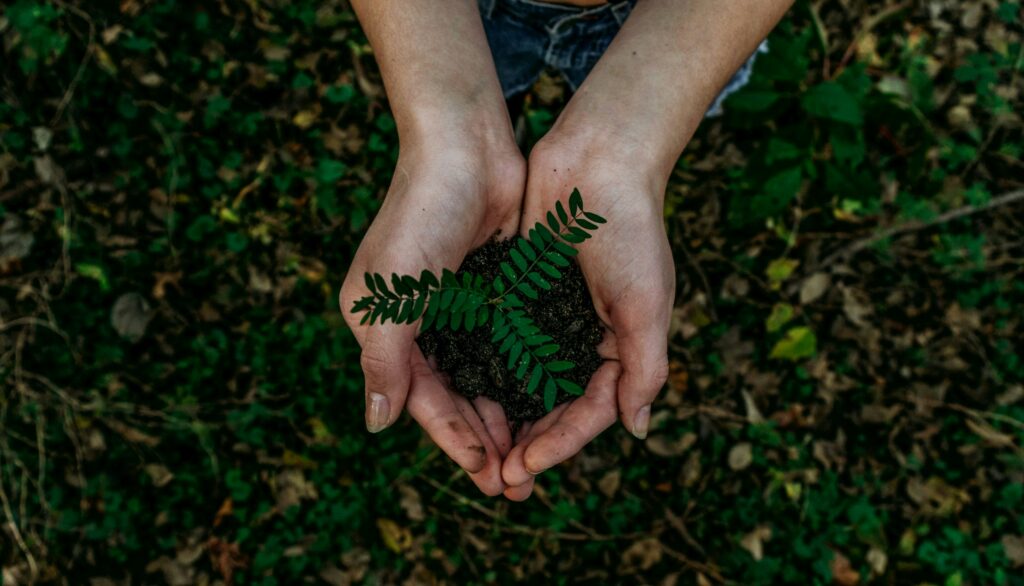
Récupération de chaleur fatale : un levier clé pour réduire les coûts
Parmi les solutions les plus efficaces pour améliorer la performance énergétique d’un site industriel, la récupération de chaleur fatale occupe une place centrale. Cette chaleur dite « fatale » correspond à l’énergie thermique inutilisée, rejetée dans l’environnement via les fumées, les eaux de refroidissement ou les effluents gazeux d’un process. Or, dans de nombreux cas, cette énergie peut être valorisée intelligemment pour préchauffer un fluide, alimenter un autre circuit thermique ou réduire la consommation d’un système auxiliaire. Ce principe repose sur une approche de bouclage énergétique, où l’on réinjecte une partie des calories perdues dans le cycle de production, à l’aide de technologies de transfert thermique performantes. La mise en place d’un tel système permet souvent de réduire de 20 à 40 % la consommation d’énergie primaire, avec un retour sur investissement généralement inférieur à deux ans. Dans une logique d’industrie circulaire et sobre, la récupération de chaleur fatale devient un levier concret pour diminuer les dépenses énergétiques, optimiser l’empreinte carbone, et sécuriser les installations contre les hausses imprévisibles du prix de l’énergie.
Quel rôle jouent les échangeurs thermiques dans les économies d’énergie ?
Les échangeurs thermiques sont les outils techniques essentiels à toute stratégie de performance énergétique. Leur rôle est de transférer efficacement la chaleur d’un fluide chaud vers un fluide froid, sans mélange et avec un rendement maximum. Dans le cadre d’un process industriel, ils permettent d’exploiter la chaleur disponible en fin de ligne, ou de récupérer l’énergie d’un fluide sortant pour la réinjecter en amont. Cette capacité à réutiliser la chaleur en interne réduit fortement les besoins en énergie extérieure, qu’elle soit issue du gaz, de l’électricité ou d’une chaudière à vapeur. L’efficacité de ce transfert dépend de plusieurs paramètres techniques : le type d’échangeur (à plaques, tubulaire, spiralé…), la surface d’échange, la différence de température entre les fluides, mais aussi le type d’écoulement (contre-courant, co-courant, croisé). Un échangeur mal dimensionné ou encrassé peut rapidement devenir un point de perte énergétique majeur. À l’inverse, un échangeur thermique performant et bien entretenu devient un atout stratégique, capable de générer des économies d’énergie durables, de prolonger la durée de vie des équipements en aval, et de contribuer activement à l’efficacité globale du système industriel.
Comment optimiser son réseau d’échangeurs thermiques (HEN)
Dans une installation industrielle, les besoins thermiques sont rarement centralisés : ils sont dispersés entre plusieurs lignes, machines ou utilités. C’est pourquoi l’optimisation d’un réseau d’échangeurs thermiques, également appelé Heat Exchanger Network (HEN), constitue un levier stratégique pour réduire la consommation énergétique globale d’un site. L’objectif est simple : utiliser au maximum les flux chauds disponibles pour couvrir les besoins en chaleur des flux froids et ainsi limiter l’usage d’énergies extérieures coûteuses. Cette approche repose sur une analyse fine des flux thermiques en présence, couplée à des outils de simulation énergétique permettant d’identifier les combinaisons les plus efficaces. En repensant l’architecture thermique d’un process, il est possible de rapprocher les sources chaudes et froides, de réduire les pertes thermiques et d’atteindre le MER (Minimum Energy Requirement), c’est-à-dire la quantité minimale d’énergie nécessaire pour faire fonctionner le système. Dans certaines industries, cette seule optimisation permet de réduire de 30 à 50 % l’apport de chaleur externe, avec un impact direct sur la facture énergétique et la rentabilité du process. Encore faut-il que les échangeurs soient correctement dimensionnés, judicieusement positionnés, et régulièrement surveillés pour garantir une performance stable dans le temps.

Étude de cas : réduction de 50 000 € par an grâce à un échangeur optimisé
Dans une usine agroalimentaire spécialisée dans la production de sauces conditionnées, l’énergie thermique représentait l’un des principaux postes de dépenses. Le process nécessitait un préchauffage de l’eau de nettoyage entre chaque lot de production, avec un recours massif à une chaudière à gaz. L’analyse thermique du site, menée par notre bureau d’études, a mis en évidence la présence d’un effluent sortant à haute température, rejeté à plus de 70 °C sans valorisation. Cette chaleur fatale, bien qu’identifiée, n’était pas exploitée par manque d’équipement adapté au transfert.
Après modélisation des flux et calculs de dimensionnement, nous avons conçu et installé un échangeur tubulaire inox à contre-courant, spécifiquement calibré pour résister à la nature chargée du fluide et aux contraintes de nettoyage en place (CIP). En récupérant la chaleur de l’effluent, l’eau de nettoyage pouvait désormais être préchauffée jusqu’à 58 °C sans apport de gaz, réduisant ainsi drastiquement le recours à la chaudière.
En un an, la solution a permis à l’entreprise de réduire sa consommation de gaz de 680 MWh, soit une économie directe de plus de 54 000 €. Le retour sur investissement a été atteint en moins de 8 mois, avec un gain environnemental équivalent à 112 tonnes de CO₂ évitées. Ce projet illustre concrètement comment un échangeur thermique bien dimensionné et intégré dans une logique de récupération peut devenir un outil de compétitivité à part entière, alliant performance énergétique, rentabilité et responsabilité environnementale.
Besoin d’accompagnement ? Eurotransfert vous aide à optimiser vos performances énergétiques
Dans un contexte industriel où chaque kilowatt compte, pouvoir compter sur un partenaire fiable, réactif et techniquement aguerri fait toute la différence. Chez Eurotransfert, nous mettons notre expertise des échangeurs thermiques et notre maîtrise des flux énergétiques industriels au service de votre performance. Notre objectif est clair : vous aider à réduire vos consommations, valoriser votre chaleur fatale et maximiser le rendement énergétique de vos procédés.
Grâce à notre bureau d’études interne, à nos solutions sur mesure et à nos interventions rapides sur site, nous accompagnons chaque projet de bout en bout : audit thermique, conception, dimensionnement, installation et maintenance. Nous travaillons main dans la main avec vos équipes pour bâtir des solutions techniques durables, adaptées à vos enjeux, et rentables dès la première année.
Vous avez un doute sur le potentiel de récupération de votre installation ? Un projet de modernisation en cours ? Un besoin de remplacement ou de retrofit d’un échangeur existant ? Parlons-en. Un simple échange peut vous faire économiser des milliers d’euros par an.
👉 Contactez notre équipe dès aujourd’hui pour bénéficier d’un premier diagnostic gratuit et découvrir comment Eurotransfert peut transformer votre chaleur perdue… en gain durable.